AI-powered Optical Solution for Real-time Bar Counting
AI • Apr 16,2024
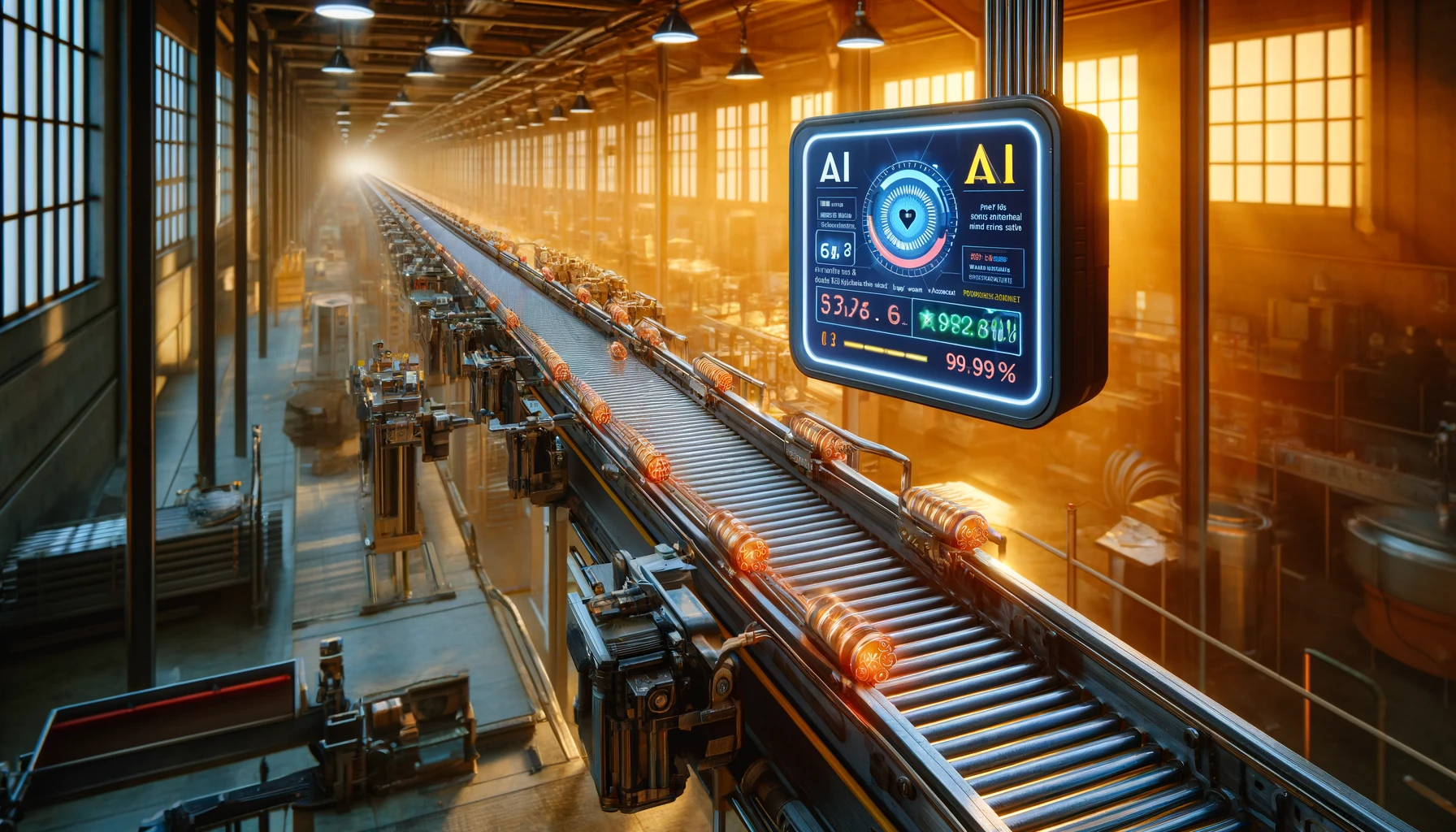
Summary:
AI-powered optical solution for real-time bar counting on conveyor belts delivers 99.99% accuracy on 8 and 10 mm diameter.
Client:
Danieli Automation is a division of the Danieli Group, focusing on process automation solutions for iron and steel facilities. Established in 1969, its primary goal is to assist the parent company by designing and developing electrical and automation equipment.
Problem Statement:
Danieli Automation sought to enhance its product portfolio for advanced plant automation, aiming to address limitations observed in existing electromechanical solutions. Seeking innovation, Danieli Automation approached beanTech to identify a solution that offered precision, contactless, and non-invasive optical technology. Additionally, the solution needed to facilitate installation without downtime and possess the capability to adapt seamlessly to production variations.
Results:
- Guarantee of worker safety.
- Reduction of manpower and spare parts in favor of a simpler setup through an Human-Machine Interface (HMI).
- 99.99% accuracy on 8 and 10 mm diameter for real-time bar counting on the conveyor belt.
- Ability to count as many as four layers at a time of products up to 20 ft (6 m) long.
- Guarantee of bars separation result.
AI Solution Overview:
Danieli Automation and BeanTech collaborated to develop DanCounter, an AI-powered optical solution for real-time bar counting on conveyor belts. This hybrid technology integrates a camera with AI and image processing algorithms. Danieli Automation created, developed, and implemented multiple AI-based applications. The AI applications were developed to estimate clogging probability in real-time and to measure steel temperature using a non-contact device. Additionally, Danieli Automation utilizes AI to improve the detection system’s performance, aiming to reduce false positives and accurately classify identified defects.
Notably, the solution is compact, requires no downtime for installation, and can be positioned at the edge of the production line. Two innermost cameras adjust their position based on the length of processed layers: positioned below the chain transfer for longer layers and rising above the chain level for shorter layers. This flexibility enhances productivity, particularly for shorter bar lengths. DanCounter facilitates automation control during separation processes, and it seamlessly reconfigures with production changes, interfacing with plant management systems. Unlike conventional solutions with counting screws, DanCounter eliminates the need for manual setup, such as changing counting screws based on product size.
References:
- ARTIFICIAL INTELLIGENCE FOR ADVANCED AUTOMATION WITH DANCOUNTER. https://www.beantech.it/wp-content/uploads/2023/04/DanCounter_Danieli_CS_ENG_compressed.pdf
- PERFECT BAR ALIGNMENT WITH NEW DANCOUNTER BUNDLING STATION. https://www.danieli.com/en/news-media/news/perfect-bar-alignment-new-dancounter-bundling-station_37_817.htm
- SUCCESSFUL USE CASE APPLICATIONS OF ARTIFICIAL INTELLIGENCE IN THE STEEL INDUSTRY. https://www.aist.org/AIST/aist/AIST/Publications/Digital%20Transformations/19-dec-digital-transformation.pdf
Industry: Metallurgy
Vendor: BeanTech
Client: Danieli Automation
Publication Date: 2023
Previos Article AI Meeting Scheduler: Save 3 Hours Weekly
Next Article AI-Powered Tax Research