Apparel Manufacturer Boosts QC & Reduced Errors with AI
A I • May 04,2024
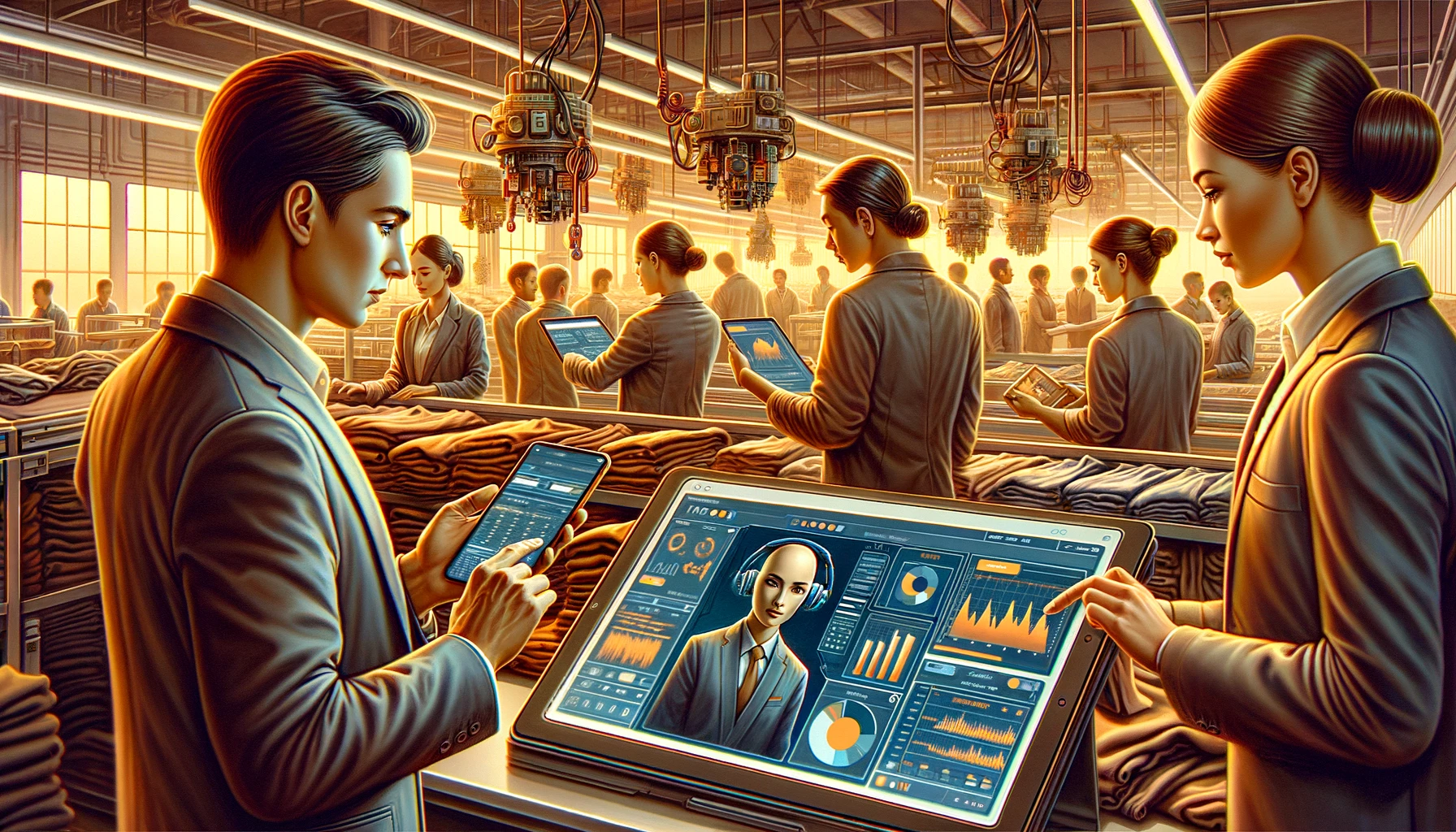
A leading apparel manufacturer faced issues with manual data, email overload, and unreliable self-inspections. They implemented an AI-powered quality control platform (Inspectorio) that streamlined communication and provided real-time analytics and automated reports. This resulted in a significant increase in QC efficiency and reduced product defects.
Client:
Gildan is a leading apparel, underwear, and socks manufacturer known for their ethical and sustainable practices. Their operations prioritize these values across 60+ global markets, partnering with vendors in Asia, Europe, and South America. They partner with vendors in Asia, Europe, and South America, while maintaining an impressive level of control—a significant 90% of their revenue comes from products manufactured in their own factories.
Problem Statement:
◉ Manual data entry and email communication slowed Gildan’s quality control, increasing errors and wasting time.
◉ Their current system required days of compiling inspection data, hindering real-time decision-making.
◉ Gildan doubted external inspectors’ product knowledge, questioning the effectiveness of their inspections.
Results:
☑️ Improved Efficiency and Reduced Defects: Gildan reports an overall increase in quality control efficiency while experiencing fewer quality issues across their factories.
☑️ Faster Issue Resolution: AI solution’s historical data access allows for quicker investigation and resolution of customer complaints, saving significant time.
☑️ Streamlined Reporting: Automated report generation eliminates manual work for QC personnel, allowing them to focus on inspections.
☑️ Data-Driven Decision-Making: AI-powered detailed performance analytics empower Gildan to make informed sourcing decisions based on real-time data.
AI Solution:
Seeking improvement, Gildan implemented Inspectorio, an AI-powered quality control platform.
Enhanced Communication and Real-Time Insights: Inspectorio centralized communication, replacing time-consuming email exchanges with a collaborative platform. Real-time analytics from Inspectorio empowered proactive decision-making based on factory performance.
Improved Self-Inspections and Automated Reports: Guided self-inspections ensured accurate data collection, boosting the process’s reliability. Inspectorio’s automated reports eliminated manual report generation.
Data-Driven Sourcing and Increased Efficiency: Data-driven insights from Inspectorio empowered smarter sourcing decisions for Gildan. Freed from manual tasks, quality control staff could focus on core inspection duties.
AI in Action:
Meet the New Inspectorio AI-Powered Platform
References:
Meet the New Inspectorio AI-Powered Platform
References:
1. Gildan Simplifies Complex Quality Control Processes with Inspectorio
Industry: Textile and Apparel
Vendor:Inspectorio
Client:Gildan
Keywords: AI for quality control, AI-powered quality management, Automated reporting, Real-time analytics
Previos Article AI Slashes Plywood Defects by 85%
Next Article AI Solution Drives 20% Defect Reduction for Food & Beverage Company