AI Solution Drives 20% Defect Reduction for Food & Beverage Company
A I • May 04,2024
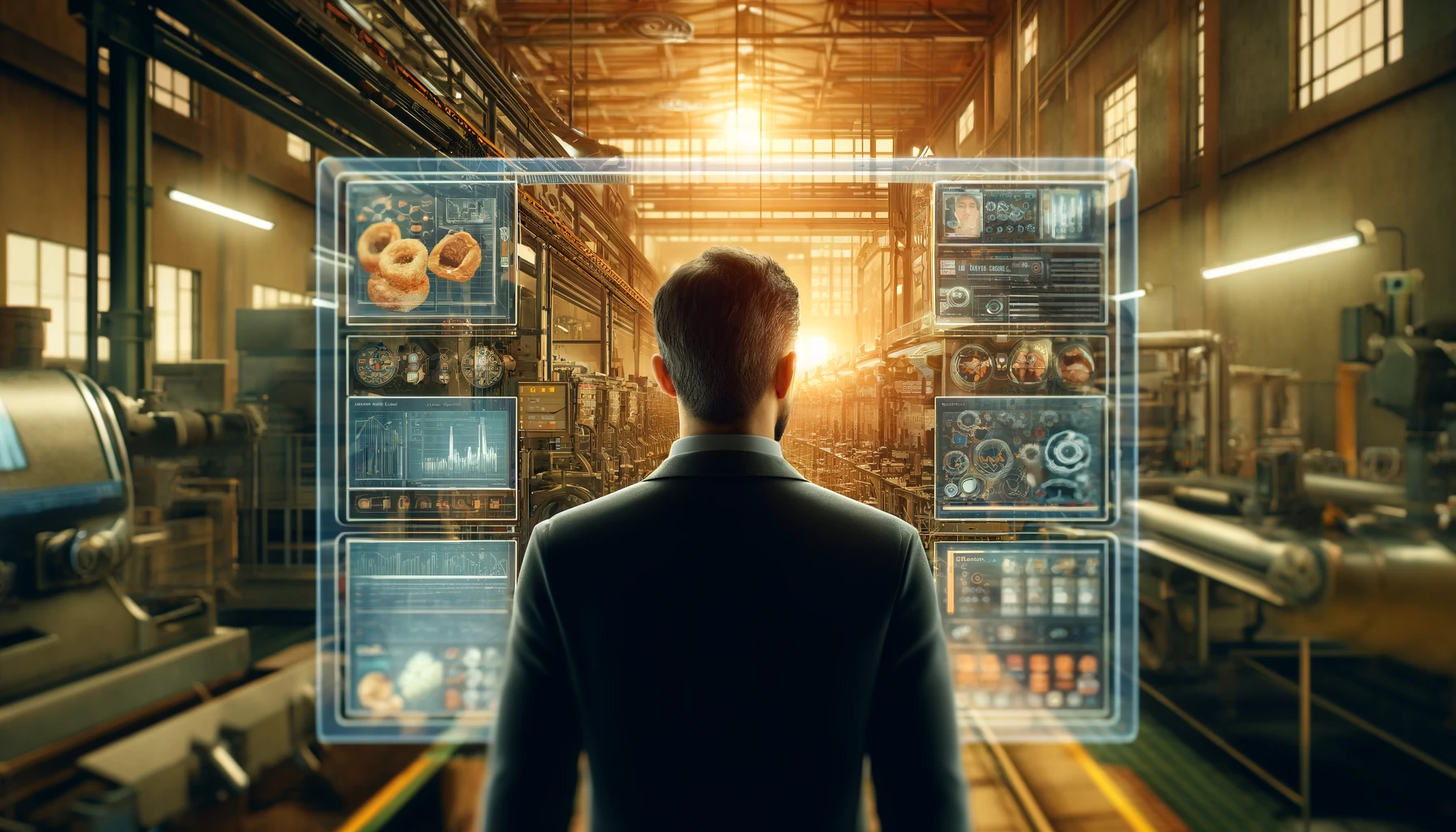
A food and beverage company struggled with a high defect rate due to a complex production process with numerous products. They implemented an AI-powered quality control solution that analyzes data from images, sensors, and customer feedback. This led to a 20% decrease in flaws, resulting in better product quality, satisfied customers, and millions saved each year from less waste.
Problem Statement:
A large food and beverage company faced the following problems:
● High defect rate: The company experienced a high defect rate due to the difficulty of manually inspecting all products in its complex production process. This led to customer concerns and lost sales.
● Inefficient quality control: The process of manually inspecting the products was not working efficiently. It was leading to defects being overlooked and the quality of the products being compromised.
Results:
☑️Reduced defects by 20%: This signifies a significant improvement in product quality, with fewer defective items reaching customers.
☑️Improved product quality: AI likely enabled consistent quality control throughout the complex production process.
☑️Increased customer satisfaction: Fewer defects likely led to happier customers and potentially increased brand loyalty.
☑️Cost Reduction: By reducing the amount of scrap and waste, the company saved millions of dollars in annual costs.
AI Solution:
Facing high defect rates due to manual inspection limitations, the food and beverage company partnered with Omdena to implement an AI-powered quality control solution.
A smart quality control system leverages machine learning to sift through a wealth of data sources.
Product Images: AI analyzes product images to identify potential defects, like visual imperfections or inconsistencies.
Sensor Data: Behind the scenes, real-time sensor data acts as a quality guardian, constantly monitoring temperature, pressure, and other critical parameters on the production line. Deviations from normal ranges can indicate potential issues.
Customer Feedback: The system incorporates customer feedback regarding product quality to identify recurring problems and areas for improvement.
By analyzing this combined data, the AI system can:
⇨ Predict Quality Problems: Leveraging historical data and identified patterns, the AI predicts potential defects before they occur.
⇨ Recommend Corrective Actions: Based on the predicted issues, the AI suggests adjustments to production processes or identifies products requiring further inspection.
Empowered by AI, the company can now pre-empt quality issues, leading to a significant reduction in defects and a more uniform product.
References:
1. AI-Enabled Quality Control Solutions for the Food and Beverage Industry
Industry: Food & Beverage Industry
Vendor: Omdena
Client: A food and beverage company
Keywords: AI for quality control, AI-powered quality management, Defect reduction, Product quality improvement
Previos Article Apparel Manufacturer Boosts QC & Reduced Errors with AI
Next Article AI Enhances Quality Control for Pharmaceutical Water