Ensuring Medical Device Safety with AI-Powered Vision
A I • May 06,2024
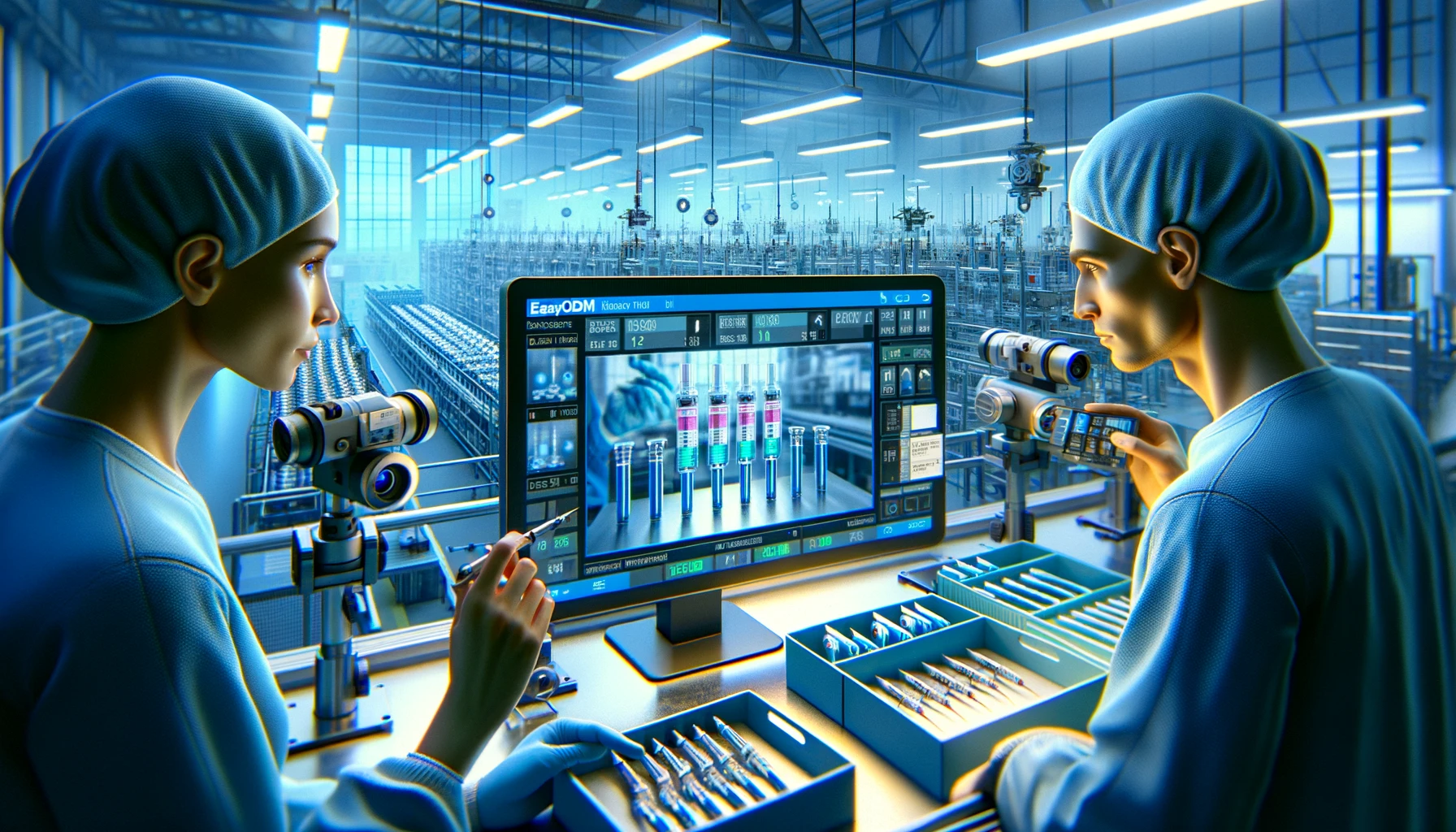
A prominent medical device manufacturer improved quality control by adopting EasyODM’s machine vision software. This AI-powered solution utilizes industrial cameras to capture images of assembled devices, enabling real-time inspection for directional label verification and tube color confirmation. This implementation has significantly reduced errors, enhanced patient safety, and cut down on recall-related expenses.
Client:
The client, a key player in the healthcare industry, is renowned for manufacturing top-quality medical equipment. Their dedication to quality control before dispatch underscores their promise of excellence. As leaders in medical technology with sustainable operations and innovative R&D efforts, they are crucial partners in advancing worldwide health outcomes.
Problem Statement:
● Quality control challenges during final assembly: The manufacturer struggled to maintain consistent product quality during the final assembly phase, particularly in verifying the correct placement of directional labels and ensuring the accurate use of plastic tube color in breathing medical devices.
● Risk of errors and safety hazards: Manual inspection methods were prone to errors, potentially leading to the assembly of faulty products. This posed a risk to patient safety, especially in cases where incorrect airflow direction could result in adverse medical outcomes.
● Potential for costly recalls and rework: Defective products could go undetected until after they were shipped, resulting in costly recalls and rework processes that disrupted operations and damaged the company’s reputation.
● Inefficient quality control processes: Manual inspection was time-consuming and labor-intensive, slowing down production and creating bottlenecks in the assembly line.
Results:
☑️ Enhanced Product Quality: Errors related to directional labels and tube color have been virtually eliminated, ensuring consistent product quality.
☑️ Improved Safety: EasyODM’s meticulous inspections safeguard patient safety by preventing critical assembly errors that could compromise proper airflow direction.
☑️ Efficiency: EasyODM’s automated system empowers operators to address issues promptly with real-time alerts, minimizing downtime and preventing the assembly of faulty products.
☑️ Cost Savings: By proactively preventing defects, the company has significantly reduced expenses associated with product recalls and rework.
AI Solution:
Seeking a more robust final assembly quality control solution, the company implemented EasyODM’s advanced machine vision software. With the help of industrial cameras strategically positioned in the final product testing zone, this AI-powered system captures images of the assembled medical devices.
The software then analyzes these images, focusing on two key aspects:
● Directional Label Verification: EasyODM ensures the presence and correct orientation of directional labels in designated locations on the device.
● Tube Color Confirmation: The system analyzes the images to confirm that the correct color of plastic tubing has been used during assembly.
The real-time inspection feature helps catch any discrepancies immediately. EasyODM notifies operators, allowing them to promptly correct errors and avoid defective products from advancing along the assembly line.
References:
1. Ai Quality Inspection In Medical Device Manufacturing: Case Study
Industry: Medical Device Manufacturing
Vendor: EasyODM
Client: Medical Device Manufacturer
Keywords: AI-Powered Quality Control, Machine Vision for Quality Control, AI in Quality Assurance, AI in Manufacturing